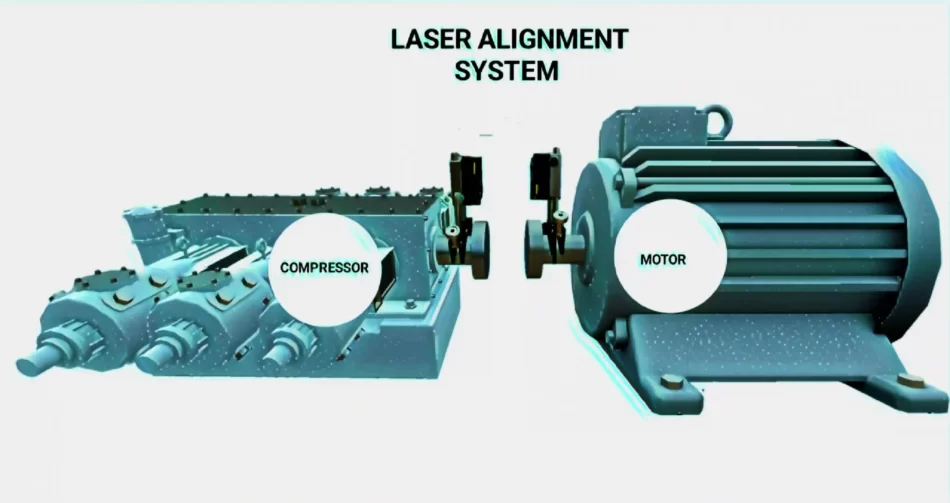
Compressor Alignment Using Laser Shaft Alignment
Table of Contents
- Introduction – Importance of compressor alignment
- To understand laser shaft alignment
- Step-by-Step Process for Compressor Alignment Using Laser Shaft Alignment
- Benefits of Laser Shaft Alignment for Compressor Alignment
- Common Challenges and Solutions in Compressor Alignment
- Maintenance and Best Practices for Long-Term Compressor Alignment
- Conclusion
- FAQs (Frequently Asked Questions)
Introduction – Importance of compressor alignment
Proper alignment of the compressor will minimize downtime and maximize efficiency. Compressors are the most important machine in many industries. If the alignment of key components like motor, coupling, compressor shaft etc. is not correct it can cause excessive vibration, severe damage and reduced overall performance.
To understand laser shaft alignment
Laser shaft alignment is a latest method for aligning rotating machinery in which misalignment are measured and corrected using laser. It gives precious readings and can adjust in real time, to ensure a good match. In this alignment process we use a laser alignment tool that emits laser light on receiver mounted on the shafts of the compressor.
Step-by-Step Process for Compressor Alignment Using Laser Shaft Alignment
- Preparation: Gather the necessary equipment, including a laser alignment tool, lifting tools, and any additional tools required for the specific compressor setup.
- Position the Laser Alignment Tool: Mount the laser alignment tool on the compressor shaft and shaft of the driven equipment.
- Initial Measurement: Activate the laser alignment tool and record the initial measurements, including angular and offset misalignments.
- Adjustments: Make adjustments to the alignment by moving the compressor until the misalignments are minimized.
- Real-Time Monitoring: Utilize the laser alignment tool to monitor the alignment adjustments in real-time, ensuring precise alignment is achieved.
- Final Verification: Once the alignment is optimized, perform a final measurement to confirm the alignment values are within the recommended tolerances.
- Documentation: Document the alignment results for future reference and to establish a baseline for future alignments.
Benefits of Laser Shaft Alignment for Compressor Alignment
Using laser shaft alignment for compressor alignment it provides several important benefits:
- Increased efficiency: Accurate configuration reduces energy consumption, improving efficiency and reducing operating costs.
- Extended compressor life: Proper alignment reduces vibration and excessive wear, extending compressor life and reducing the need for maintenance
- Reduced downtime: Accurate scheduling reduces the risk of unexpected and unplanned downtime, increasing overall productivity.
- Improved safety: Proper configuration creates a safer work environment by reducing the potential for mechanical failures and associated hazards.
- Time and cost savings: Laser shaft alignment enables faster alignment procedures, saving valuable time and reducing labor costs.
Common Challenges and Solutions in Compressor Alignment
While compressor alignment using laser shaft alignment offers numerous advantages, it is essential to be aware of potential challenges and their solutions:
- Restricted Access: Limited space and difficult-to-reach components may pose challenges during alignment. In such cases, specialized laser alignment tools with flexible measurement options can be utilized.
- Thermal Growth: Temperature variations can cause thermal growth, leading to misalignment.
- Soft Foot: Soft foot refers to uneven contact between the machine and its base, which can affect alignment accuracy. Detecting and correcting soft foot conditions before alignment is crucial for accurate results.
- Maintenance Practices: Regular monitoring, preventive maintenance, and timely realignment are important to sustaining proper compressor alignment and maximizing equipment performance.
Maintenance and Best Practices for Long-Term Compressor Alignment
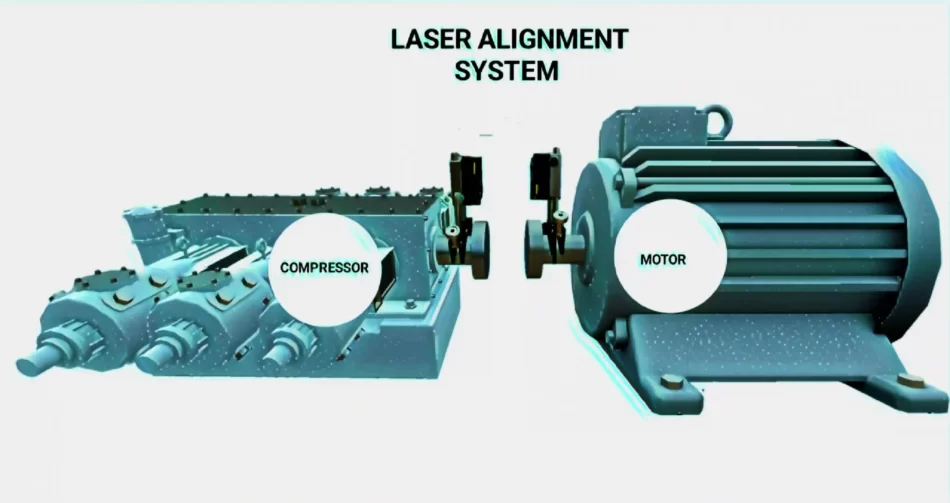
To ensure long term compressor alignment, follow this maintenance and best practices:
- Regular Inspections: Conduct routine inspections to identify any signs of misalignment or excessive vibrations.
- Lubrication: Proper lubrication of bearings and other rotating parts reduces friction and wear, contributing to better alignment and prolonged equipment life.
- Alignment Checks: Schedule periodic alignment checks to detect and correct any misalignments promptly.
- Alignment Records: Maintain detailed records of alignment measurements, adjustments, and maintenance activities for reference and analysis.
Conclusion
All compressor need perfect alignment to increase performance, reduce downtime, and extend machine life. Laser shaft alignment provides a more accurate and efficient way to align compressors, it provide many benefits for the machine such as increased efficiency and reliability, reduced maintenance, improved safety and achieve significant cost reductions.
FAQs (Frequently Asked Questions)
- 1. Why is compressor alignment important?
- Proper compressor alignment will provide maximum efficiency, energy efficiency and extends machine life by reducing vibration and wear.
- 2. How does laser shaft alignment work?
- Laser shaft alignment uses laser transmitter and receiver to measure the offset, angular and correct misalignment in rotating parts.
- 3. What are the advantages of laser shaft alignment?
- Laser shaft alignment increases productivity, extends machine life, reduces downtime and saves time.
- 4. How often should compressor alignment be checked?
- Periodic consistency checks are recommended to quickly identify and resolve discrepancies.